Parte 1: Equipo y piezas de suspensión automotriz
1. Proceso de mecanizado de engranajes
De acuerdo con los diferentes requisitos estructurales, el principal proceso tecnológico del procesamiento de piezas de engranajes es la forja de espacios en blanco → la normalización → el mecanizado de acabado → la conformación de engranajes → el biselado → el tallado → el afeitado → (soldadura) → el tratamiento térmico → el rectificado → el recorte de malla.
Los dientes generalmente no se mecanizan después del calor, excepto los dientes principales y secundarios o las piezas que el cliente requiere para rectificar los dientes.
2. Flujo de proceso del eje
Eje de entrada: palanquilla de forja → normalización → mecanizado de acabado → laminado de dientes → taladrado → modelado de dientes → biselado → tallado → afeitado → tratamiento térmico → rectificado → recorte de malla.
Eje de salida: palanquilla de forja → normalización → mecanizado de acabado → rectificado y tallado → afeitado → tratamiento térmico → rectificado → ajuste de emparejamiento.
3. Flujo de proceso específico
(1) Billete de forja
La forja en caliente es un proceso de forja en blanco ampliamente utilizado para piezas de engranajes de automóviles. En el pasado, la forja en caliente y la extrusión en frío eran ampliamente utilizadas. En los últimos años, la tecnología de laminado de cuña transversal se ha promocionado ampliamente en el procesamiento de ejes. Esta tecnología es especialmente adecuada para fabricar piezas brutas para ejes escalonados complejos. No solo tiene alta precisión, pequeñas asignaciones de procesamiento posterior, sino también una alta eficiencia de producción.
(2) Normalización
El propósito de este proceso es obtener la dureza adecuada para el posterior corte de engranajes y preparar la estructura para el tratamiento térmico final, a fin de reducir efectivamente la deformación del tratamiento térmico. La normalización general se ve muy afectada por el personal, el equipo y el medio ambiente, lo que dificulta el control de la velocidad de enfriamiento y la uniformidad de la pieza de trabajo, lo que da como resultado una gran dispersión de la dureza y una estructura metalográfica desigual, lo que afecta directamente el mecanizado y el tratamiento térmico final.
(3) Mecanizado de acabado
Con el fin de cumplir con los requisitos de posicionamiento del procesamiento de engranajes de alta precisión, se utilizan tornos CNC para el acabado de piezas en bruto de engranajes. El orificio interior y la cara del extremo de posicionamiento del engranaje se procesan primero, y luego el procesamiento de la otra cara del extremo y el diámetro exterior se completan simultáneamente. No solo garantiza los requisitos de verticalidad del orificio interior y la cara del extremo de posicionamiento, sino que también garantiza que la dispersión de tamaño de la producción de dientes en bruto a gran escala sea pequeña. De este modo, se mejora la precisión de la pieza en bruto del engranaje y se asegura la calidad de procesamiento de los engranajes posteriores.
Hay tres formas principales de posicionamiento y sujeción para el procesamiento de piezas de eje:
1. Posicionamiento con el orificio central de la pieza de trabajo: en el procesamiento del eje, la coaxialidad de cada superficie exterior y cara final de la pieza, y la verticalidad de la cara final con respecto al eje de rotación son los elementos principales de su posición mutua precisión. La base de diseño de estas superficies es generalmente Ambos son la línea central del eje. Si se utilizan dos orificios centrales para el posicionamiento, se cumple el principio de coincidencia de la referencia.
2. El círculo exterior y el orificio central se utilizan como referencia de posicionamiento (una abrazadera y una parte superior): aunque la precisión de centrado es alta, la rigidez es baja, especialmente cuando se procesan piezas de trabajo más pesadas, no es lo suficientemente estable y el corte cantidad no debe ser demasiado grande. Durante el mecanizado de desbaste, para mejorar la rigidez de la pieza, la superficie exterior del eje y un orificio central se pueden utilizar como referencia de posicionamiento para el procesamiento. Este método de posicionamiento puede soportar un gran momento de corte y es el método de posicionamiento más común para las piezas del eje.
3. Utilice las dos superficies circulares exteriores como referencia de posicionamiento: al mecanizar el orificio interior del eje hueco (por ejemplo: mecanizar el orificio interior del cono Morse en la máquina herramienta), el orificio central no se puede utilizar como referencia de posicionamiento. , y las dos superficies circulares exteriores del eje se pueden utilizar como referencia de posicionamiento. dato de posicionamiento. Cuando la pieza de trabajo es el husillo de la máquina herramienta, los dos diarios de soporte (referencia de ensamblaje) se utilizan a menudo como referencia de posicionamiento, lo que puede garantizar la coaxialidad del orificio cónico en relación con el diario de soporte y eliminar el error causado por la desalineación. de los datos.
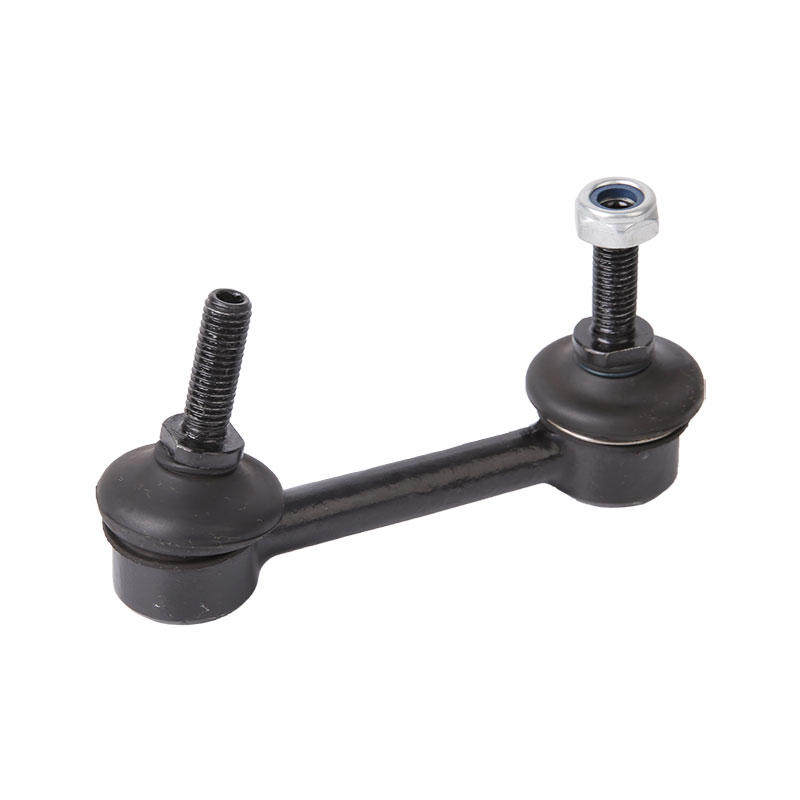
Parte II: Partes de la carcasa
1. Flujo de proceso
El flujo general del proceso es fresado de la superficie de la junta → orificios del proceso de mecanizado y orificios de conexión → orificios de los cojinetes de mandrinado en bruto → orificios de los cojinetes de mandrinado fino y orificios de los pasadores de ubicación → limpieza → detección de prueba de fugas.
2. Método de control
(1) Accesorios
El proceso de mecanizado de la carcasa de la transmisión se toma como ejemplo de "Mecanizado del centro de mecanizado vertical. Proceso 10# Proceso de mecanizado del centro de mecanizado vertical Proceso 20# Mecanizado del centro de mecanizado horizontal Proceso 30#", se requieren tres conjuntos de accesorios del centro de mecanizado para evitar piezas de trabajo. También se debe considerar la deformación de la sujeción, como la interferencia de la herramienta, la operación flexible, las piezas múltiples y una abrazadera, y el cambio rápido.
(2) Aspecto de la herramienta
En el costo de fabricación de autopartes, el costo de la herramienta representa del 3% al 5% del costo total. La herramienta compuesta con estructura modular tiene las características de alta precisión, portaherramientas reutilizable y pequeño inventario, y es ampliamente utilizada. Puede acortar en gran medida el tiempo de procesamiento y mejorar la eficiencia laboral. Por lo tanto, cuando los requisitos de precisión no son altos y las herramientas estándar pueden lograr mejores resultados de procesamiento, las herramientas estándar deben usarse tanto como sea posible para reducir el inventario y mejorar la intercambiabilidad. Al mismo tiempo, para piezas producidas en masa, el uso de herramientas compuestas no estándar avanzadas para piezas con requisitos de alta precisión puede mejorar la precisión del mecanizado y la eficiencia de producción.